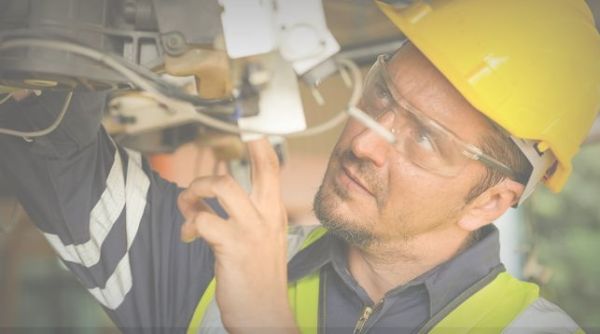
Definiciones:
Mantenimiento proactivo: un tipo de mantenimiento basado en condición que enfatiza la detección y corrección rutinaria de las causas raíz que de otro modo provocarían fallas. Las causas raíz como la alta contaminación del lubricante, la alineación y el balanceo se encuentran entre las más críticas.
Mantenimiento predictivo: un tipo de mantenimiento basado en condición que enfatiza la predicción temprana de fallas utilizando técnicas no destructivas como análisis de vibraciones, termografía y análisis de partículas de desgaste.
El funcionamiento eficiente de la maquinaria industrial depende de dos estrategias de mantenimiento fundamentales: el mantenimiento proactivo y el mantenimiento predictivo. Si bien ambos enfoques se enmarcan en el concepto más amplio de mantenimiento basado en condición, sus metodologías e impactos son distintos y complementarios.
Este artículo tiene como objetivo desmitificar estos conceptos, comprender claramente cómo funciona cada estrategia, su importancia en el ámbito del mantenimiento y cómo representan en conjunto una defensa sólida contra fallas de las máquinas e ineficiencias operativas. Veremos cómo optimizar las prácticas de mantenimiento para mejorar la longevidad y la confiabilidad de las máquinas explorando sus funciones, beneficios y retos.
Mantenimiento predictivo: detección de fallas (señales tempranas)
En la vida diaria de una máquina lubricada típica, puede existir un desgaste sutil que aumenta silenciosamente, sin que lo sepan los operadores y los equipos de mantenimiento. Al principio de este modo de falla, el inicio de la falla (I) es prácticamente imperceptible. Pero a medida que continúa y el desgaste progresa gradualmente, los síntomas se vuelven medibles y se alcanza el punto de detección de falla (P).
Con la estrategia correcta que incluye la frecuencia del monitoreo de condición, la detección de fallas se encuentra más cerca de su inicio. Este es un objetivo crucial del mantenimiento predictivo: detectar los signos de falla lo antes posible.
Sin embargo, si la falla no se detecta correctamente, con el tiempo la máquina experimentará un desgaste suficiente como para que ya no pueda realizar su trabajo y se alcance el punto de Falla Funcional (F) , con el correspondiente impacto en la producción. La falta de detección puede deberse a varias razones, pero la mayoría de las veces se debe a un monitoreo poco frecuente, herramientas inadecuadas o falta de capacitación adecuada. Cuando esto no se controla, sigue la Falla Catastrófica (Muerte) , por la cual la máquina puede parar y producir daños colaterales a partir de este punto.
Las etapas que se describen aquí se ilustran mediante la curva PF en la figura 1. Tradicionalmente, la curva PF recibe su nombre por la asociación de las condiciones de monitoreo con los modos de falla conocidos entre la detección de la falla (P) y la falla funcional (F). La predicción de fallas con detección temprana requiere la estrategia de mantenimiento predictivo adecuada. Cada modo de falla puede tener una curva PF corta o larga.
A medida que la curva desciende de izquierda a derecha, el desempeño de la máquina (eje y) se ve afectado negativamente. La falla de la máquina se vuelve más grave a medida que pasa el tiempo (eje x) y los síntomas de la falla de la máquina son más fáciles de detectar. Pero, si bien esta mayor detección parece algo bueno, lamentablemente coincide con un inminente tiempo de inactividad y mayores costos, ya que el daño es irreparable.
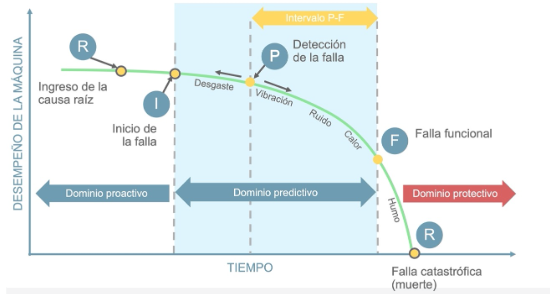
Figura 1. El El dominio del mantenimiento predictivo en el intervalo P-F
Mantenimiento proactivo: detección antes de la falla (causa raíz)
Toda falla de una máquina es consecuencia de las acciones que la precedieron. En otras palabras, lo que hacemos o dejamos de hacer en el mantenimiento y las operaciones es lo que finalmente conduce al inicio de la falla. Aquí es donde se pone a prueba la confiabilidad de la máquina. ¿Confiamos en la robustez de la máquina o configuramos cuidadosamente nuestras máquinas para el éxito? ¿Realmente estamos haciendo todo lo posible para retrasar la aparición de la falla el mayor tiempo posible, al menos hasta el punto en que los costos lo justifiquen?
El veredicto de décadas de estudios de grupos de usuarios, fabricantes de equipos originales e institutos de investigación sobre las razones más comunes por las que fallan los rodamientos y otros componentes de las máquinas es que existe consenso en que la lubricación deficiente y el insuficiente control de la contaminación están en la parte superior de la lista de causas raíz. Su introducción está marcada por el punto de inicio de la causa raíz (R). La brecha entre el inicio de la causa raíz y el inicio de la falla es un factor de gravedad de la causa raíz, sensibilidad del componente y tiempo de gestación.
Éste es el objetivo crucial del mantenimiento proactivo: detectar y corregir las condiciones que causan problemas y que de otro modo provocarían fallas.
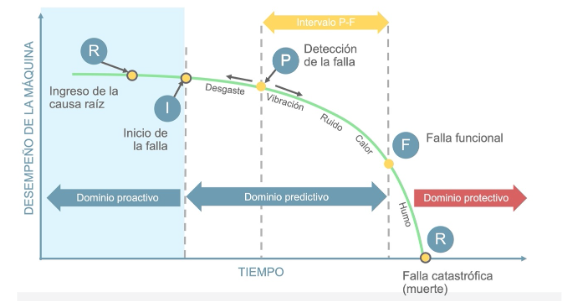
Figura 2. El dominio del mantenimiento proactivo en el intervalo P-F
Adopción de estrategias de mantenimiento basado en condición
El mantenimiento predictivo se ha vuelto más común en las instalaciones industriales con la adopción de tecnologías de monitoreo de condición como análisis de vibraciones, termografía y monitoreo de desgaste. Particularmente cuando la tecnología de sensores en tiempo real y la infraestructura del Internet de las Cosas (IoT, por sus siglas en inglés) han acelerado la implementación. Las mejores estrategias de mantenimiento predictivo son aquellas en las que se monitorea la detección incipiente de fallas.
Cuando se toman medidas correctivas rápidas, se puede minimizar el impacto que tiene la falla en los costos de reparación y la duración del tiempo de inactividad.
El mantenimiento proactivo también ha recibido una mayor atención, con un enfoque en las estrategias de control de la contaminación y el monitoreo de contaminantes y propiedades de fluidos con análisis de aceite. Esto se atribuye, en parte, a una mejor educación que saca a la luz el impacto oculto que tienen los contaminantes y las pequeñas deficiencias de lubricación en la confiabilidad de las máquinas. Cuando se toman medidas correctivas dentro de este dominio, se reduce la cantidad de fallas y se aumenta la vida útil de las máquinas.
Por ello, las mejores estrategias se centran en el monitoreo de condición lo más a la izquierda posible de la curva PF; es ahí donde se logran mayores ahorros de costos. Pero, al mismo tiempo, esto se ve desafiado por el enigma de la acción correctiva. Cuando se detectan tempranamente síntomas de falla en el dominio predictivo, a menudo se les cuestiona y la acción correctiva no se aplica debido a una señal débil.
Este suele ser el caso de las partículas de desgaste en etapa temprana detectadas con el análisis de aceite. Si bien es eficaz para detectar esta débil señal de manera temprana, la máquina parece funcionar normalmente y la acción correctiva puede demorarse a medida que se solicita una mayor confirmación del modo de falla. Pero a medida que la señal se vuelve más fuerte y más obvia, también lo hace la proximidad a una falla funcional o catastrófica.
Esto se hace aún más evidente en el ámbito proactivo, donde el monitoreo de condición detecta un problema de contaminación o con las propiedades del lubricante. Sin que se produzca una falla (aún), surgen preguntas y se postergan las acciones, a pesar de que se hayan tomado medidas correctivas relativamente simples, como la filtración o los cambios de lubricante.
Todo esto se puede abordar con una educación adecuada para crear conciencia sobre las estrategias de mantenimiento proactivo como complemento coherente al mantenimiento predictivo, junto con un poco de evidencia de primera mano.
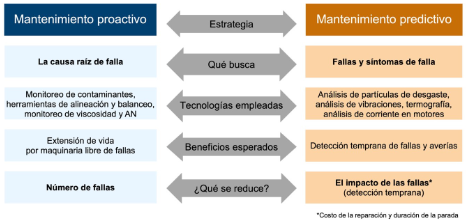
Figura 3. El mantenimiento basado en condición
En la práctica, tanto el mantenimiento proactivo como el mantenimiento predictivo pueden llevarse a cabo en paralelo como una estrategia de mantenimiento basada en la condición (CBM, por sus siglas en inglés). No se debe asumir que el mantenimiento proactivo es la solución por sí solo.
De hecho, hay muchas causas raíz que pasan desapercibidas con los enfoques típicos de mantenimiento proactivo. En cambio, está diseñado para abordar el 20 % de las causas raíz de fallas responsables del 80 % de los casos de fallas (regla 80:20).
Dicho esto, el mantenimiento predictivo puede ayudar a detectar la mayoría del 20 % restante. Y dado que tanto el mantenimiento proactivo como el predictivo se centran en el control de las condiciones, se pueden seguir con gráficos adyacentes e indicadores clave de desempeño (KPI, por sus siglas en inglés).
En el caso de máquinas individuales, las condiciones de causa raíz proactivas pueden ser «indicadores principales» (que indican lo que sucederá) junto con los síntomas de falla predictiva que pueden considerarse «indicadores rezagados» (que indican lo que acaba de suceder). De la misma manera, el cumplimiento del programa de mantenimiento puede ser un indicador principal y el tiempo de inactividad programado/no programado puede ser un indicador rezagado como un KPI de toda la planta.
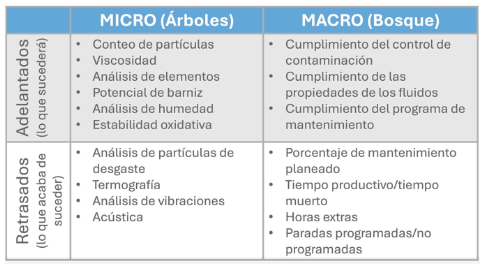
Figura 4. Indicadores clave de desempeño
Potencie su estrategia de mantenimiento con los conocimientos y las soluciones de vanguardia de Noria Latin America. Ya sea que esté buscando implementar prácticas de mantenimiento proactivas o predictivas, nuestro equipo de expertos está listo para guiarlo en cada paso. Visite Noria para descubrir una gran cantidad de recursos, programas de capacitación y servicios de consultoría diseñados para mejorar sus operaciones de mantenimiento. Permítanos ayudarlo a transformar su enfoque en la confiabilidad y eficiencia de las máquinas: ¡comience su viaje hoy mismo!
Bennett Fitch, Noria Corporation. Traducción por Roberto Trujillo Corona, Noria Latín América